かわさきマイスター活動レポート
ものづくりの現場から学ぶ
川崎市では平成9年から極めてすぐれた技術や技能を発揮して市民生活に寄与している現役の技術・技能者を「かわさきマイスター」に認定し、その技の次世代への継承や振興活動を行っています。川崎区藤崎に本社を置く部品加工会社、株式会社クレールには大橋明夫さんと平賀正明さんのお二人のかわさきマイスターが在社しています。10月29日(木)、同社を今年度(2009年度)採用の川崎市職員が新規採用職員研修の一環として訪れました。
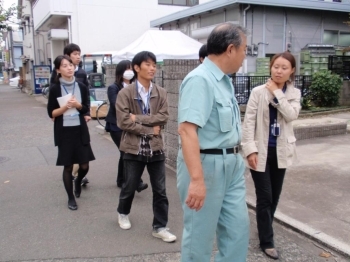
新規採用職員研修の一環として株式会社クレールを12名の今年度採用の川崎市職員が訪問。
新規採用職員研修はこの春に続いて2度目。300名以上いる新しい市職員が30班ほどにわかれ、川崎市について自ら調べ、実際にまちを歩き体験することで、自らの働くエリアや市民の皆様のことを学ぼうという研修です。当日同社を訪れたのは川崎大師地区を選んでまち歩き研修を行った所属や職種も様々な12名のグループですが、体験を今後の市民サービスの中で反映したいという意気込みに、マイスターの大橋さんと平賀さんも、工場を案内しながら熱心に作業の説明をしたり研修生の質問に答えるなどしたりして終始、意欲的な応対をして歓迎しました。
かわさきマイスターの熟練された高度な技術
株式会社クレールは自動車やコピー機などの部品作りに携わっている会社です。同社のような大手メーカーの部品作りを請け負っている会社は、日本の産業の下支えの役割を担ってきているという点からも極めて存在意義の高いものです。例えば自動車メーカーなど自社ですべての部品を作るわけではなく、大部分をいろいろな技術力を持った会社に発注してそれを組み立てています。しかし、厳しい経済状況の下、海外への工場移転や廃業などにより年々数が減少、川崎市でも平成10年には約2500社あったあった製造業の会社がこの10年で約1,750社まで減ってしまったといいます。そんな中、株式会社クレールは2人のかわさきマイスターをはじめとする社員の皆さんの努力により、先端技術を誇る高精度な設備でさまざまな業種の製品に対応できる部品加工のできる会社として、川崎の地で頑張っています。また、同社はおよそ50名の社員をかかえていますが、雇用という面でも地域に大きな貢献をしています。
■株式会社クレール本社:神奈川県川崎市川崎区藤崎3-14-2
工場:神奈川県川崎市川崎区藤崎1-28-9
TEL:044-244-5231
FAX:044-299-3958
URL:
http://www.clr.co.jp 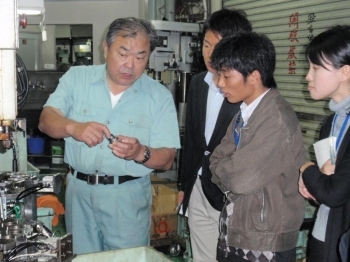
高品質、低コストを考え大橋さんが独自で設計した金型で難易度の高い加工品を製作しています。
平成11年度のかわさきマイスターに認定された大橋明夫さんは、プレス順送の金型の設計製作に熟練された技術を持っています。製品を作る時には、プレス機に上下に分かれた金型を着け、金型の間に材料を入れて上下に挟み込んで作ります。普通ですと工程が10ある場合、金型は10個必要になりますが、順送は10工程が1個の金型に組み込まれています。そのため大変複雑な構造の型になり、蓄積された知識と経験を伴った高度な技術が要求されます。高品質と低コストを考えた大橋さんの設計した金型があってはじめて難易度の高い加工品を製作できるのです。
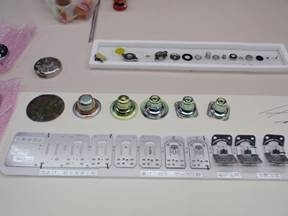
プレス順送の製作過程。
左の型から右側の型に順にプレスされて行き製品が完成します。
下から2段目左端のように、お客さんからは平たい金属板1枚と進行の図面が来るだけです。現在はパソコンで3D画像を描くことができますが、大橋さんは40年以上も前から頭の中だけで図面を理解し工程を浮かべてきました。
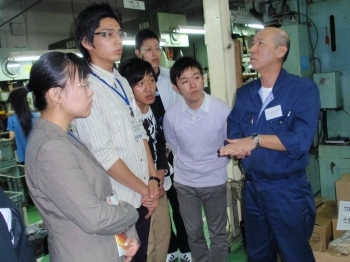
丁寧に説明する平賀さん。
平賀正明さんは生産システムの設計・製作で平成20年度のかわさきマイスターに認定されました。加工する際に部品や工具の作業位置を指示・誘導するために用いる治具というものは、どの作業者が作業しても同一の作業位置を確保できるなど、同一製品を大量に作るに必要な器具で、平賀さんはその設計・製作などの分野で高い技術を持っています。例えば、なにかの機械を加工して別のものを作るばあい、元の機械に金具等を入れて製品を生産しやすくしたり、個々の製品に合うような装置を作るなどしたりする場合に平賀さんの優れた技能と技術が発揮されます。
2人のマイスターの案内で工場見学
清水社長さんやマイスターお二人によるクレールの会社概要などの説明の後、研修生は2班に分かれ、それぞれ大橋さんと平賀さんの案内で実際の作業現場を見学しました。
同社の50人の従業員のうち女性は年配の方を中心に30人。工場内では女性の作業風景が目を引きました。そのため見学者からは女性が多いのは力を使わなくても作業できるようなシステムができあがっているのかという質問もでました。平賀さんの作る優れた治具により負荷が少なく効率よく製品を作ることができるとのことです。大橋さんも平賀さんも試作品の段階から実際に使用する人の意見を吸い上げ改善につなげていく努力をしているのです。
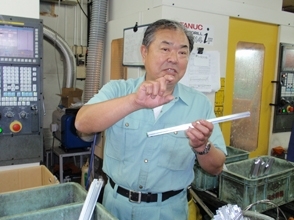
アルミ押し出し材の説明をする大橋さん。同社にはアルミ材は2メートルくらいの長さで搬入されますそれを所定の寸法に切りそろえ、機械にのせ肉を削り、そのあとプレスで穴を掘っていきます。
コピー機の残留トナーを除去する部品は単価が安くクレールの人気製品の一つです。A1サイズのコピー機のブレード部分のゴムの先端でドラムに付着した粉をかき分けますが、長さ960ミリくらいのブレード部にコンマ1ミリくらいのゴムの稜線を張り付けるのは大変な作業。そういう細かい作業は女性のほうが向いているとのことです。10万台分の注文に対し、当初は1日50本程度だったものが、平賀さんの創意工夫により現在は1000本くらい生産可能になっています。
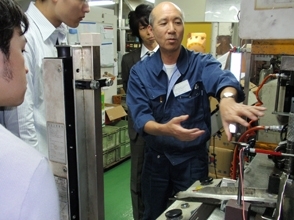
順送金型の説明をしています。
平賀さんによると製品をラインに乗せるのにどのくらい時間がかかるかといった納期の問題は、金属を切る刃物の歴史と関係していると言います。先輩たちは金属板に穴をあけるにあたって最初はドリルでたくさんの小さな穴をあけてから鏨(たがね)で切り、ヤスリで仕上げました。それには3ヵ月から半年の時間がかかっていたそうです。それからコンターマシンという、のこぎり刃のついた輪状の工具で押し切って穴をあけるという時代を経て、現在ではワーヤーカットという機械を使い、1時間で切り抜いてしまうとのことです。
「便利にはなりましたが、ちょっとせせこましいですね」と平賀さんは笑いながら説明してくれました。
設備の組み立てには1月以上かかります。その間に高精度なものを作るために施行を重ねます。実際に生産ラインに乗るのには1年から1年半のスパンを取るということです。
工場見学後、研修生全員から活発な質問が
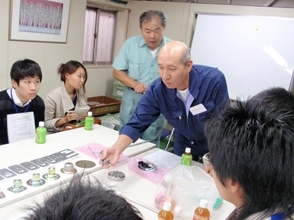
研修生全員から活発な質問が。時には製品を示しながらていねいに応答を。
現場の見学が終わったあと、質疑応答にはいりました。研修生全員から市民サービスの担い手にふさわしい活発な質問がでました。
その一つ「川崎で事業をしていく魅力は」という質問に対してお二人は、「材料を作るメーカーが近隣にあり、物流インフラも整備されているため、すばやく加工に着手することができる」という利便性をあげていました。
また、首都圏ということでさまざまな技術に関する展示会などにも行きやすいということもあります。例えば国際見本市などが開かれる東京ビッグサイトまで車で30分で行け、忙しい中、日帰りで勉強できるなどの利点もあげていました。お二人は仕事に関連したイベントだけでなく食品や包装などできる限り他職種のものも見学にいくようにして常に新しい情報を拾っているとのことで、その中からアイデアが浮かぶこともあるそうです。
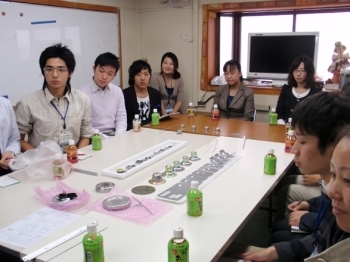
お二人の応答に研修生は熱心にききいっていました。
逆に「デメリット」については、近隣への騒音をあげました。以前は周辺にクレールのような大手企業の部品作りをしている会社は多くありましたが、いまではクレールが一番大きいとのこと。代わりに周囲に一般住宅が増えてきたという環境の中で、いかに騒音を抑えていくかということは、同社だけでなく住宅地にある加工会社の共通の課題だといえます。
現在生産しているものは1,2年後には変わっていきます。生産ラインに乗った瞬間から次の新しい製品を探さなければならないといいます。また、以前のように特定のお客さんの仕事をこなしていれば、次から次へと仕事が派生していくという時代ではなくなりました。そのような状況下で、これからも川崎の地に根付きながら日本の産業を支え地域に貢献していくために、かわさきマイスターの大橋さん、平賀さん、そして株式会社クレールの皆様は日々努力していらっしゃいます。そして、川崎市役所新人職員は、この貴重な体験を市民サービスに反映してくれるはずです。